Rapid Drug Manufacturing Scale-Up: Best Practices
As pandemic conditions persist, the pharma industry continues to respond as rapidly as possible to bring more vaccine options to the global population.
But developing one or more effective vaccines was just the first hurdle to clear. The drug industry is facing challenges of producing sufficient quantities of any successful vaccine in order to supply the global demand.
To say that deadlines are tight is an understatement. Scaling up quickly has tested the limits of every stage of the process – from developing and securing supply chains, to bringing new equipment online and validation.
To learn more about the challenges and best practices associated with scaling up quickly, Pharmaceutical Technology recently contacted leading API and equipment manufacturers, as well as contract development and manufacturing organizations. Curia Vice President of Global Chemical Development, Sripathy Venkatraman, was one of the experts PharmTech consulted for this article published in late 2020.
Here are some of the key difficulties and best practices for rapid drug manufacturing scale-up outlined in the article, along with additional insights from our team.
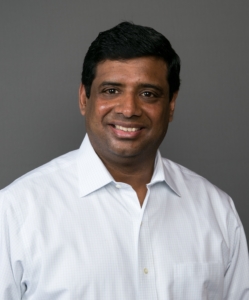
The Challenges of Rapid Scale-Up
Ensuring continuous quality and safety and compliance is the top consideration during the development of any drug, and accelerating process scale-up can increase the likelihood of failure. Small-scale experiments, for example – especially those relating to process safety – may not provide sufficient data to identify flaws or risks that can emerge at larger production levels. Some of these risks include:
- Impurity Profiles
It is critical to understand impurity profiles, and how they are likely to translate at scale. Shorter timelines can affect both process development and understanding of the edge of failure — the point where a batch fails to meet acceptable criteria — which is important for transfer. For example, not understanding mass and heat transfer can result in the need to repeatedly rework batches in order to meet specifications. - Supply Chain Security
The need for robust supply chains is a growing pharma industry concern and securing adequate supplies of raw materials is only one piece of the puzzle. It’s also important to have sufficient quantities of API available ahead of time for process qualification, and to establish sufficient history with each vendor to verify the consistent quality of the materials they provide. - Other Challenges
Other challenges include the need to maintain (or increase) the transparency of customer communications during lockdown conditions, weighing the pros and cons of different manufacturing technologies, and the unique challenges of scaling therapies with less-established platforms (notably viral vaccines under current conditions).
Strategies for Successful Scale-Up
One of the most common mistakes made under tight timelines is to push analytical method development to the very last stage. But to succeed in rapid scale-up, you need to move quickly to understand the edge of failure for critical process parameters once a process is set. A better approach is to run process development and analytical method development in parallel, rather than sequentially.
Another strategy relates to availability of raw materials and identifying suppliers early on. You must qualify suppliers and set specifications for materials as early as possible during development in order to have a clear understanding of critical quality attributes.
Having a contract development and manufacturing partner with a strong and well-qualified domestic and international team helps to ensure quality results and prevents many costly delays. Experienced teams know how to plan effectively, build quality into every stage, use equipment most effectively and perform process design correctly at smaller scales. Groups like these not only minimize potential issues when scaling up, they can also troubleshoot more efficiently when challenges arise at larger scales.
Leveraging Equipment
There is often a disconnect between early research & process development and later pilot & commercial production – notably with the types of equipment used during process scale-up. To avoid these problems, process development must be carried out with the capabilities of the validated manufacturing equipment in mind. For example, knowing early on whether the manufacturing process will use a centrifuge or a pressure-filter dryer – or whether the process will call for a Hastelloy versus a glass-lined reactor – can reduce unnecessary complications.
Bottlenecks and surprises can be largely minimized by getting engineering input during the process phase. In addition, process simulation software can be very helpful in early evaluations of existing equipment performance.
Streamlining the Process
Because time constraints frequently limit the number of experiments, those that are performed should generate the most relevant data possible in the available timeframe. The more data-rich the experiment, the more likely it will be able to minimize or mitigate risk during scale-up. This requires advanced technologies capable of capturing large amounts of data in one shot, speeding up process research without sacrificing quality.
A design-of-experiments (DoE) approach — which is critical to understanding the effects of different variables on a process — can give you a very important understanding of which variables may influence or alter a given reaction. This can take on heightened importance when process development is streamlined or time-constrained. Modeling and simulations are also helpful in predicting and addressing issues which can’t be gleaned from small-scale experiments.
While every process is different, any scale-up project can be enhanced by advanced planning and relationship building. Effective team building, vendor management, proactive equipment and technology acquisition, simulations, and efficient communication can all play a role in ensuring your success.
To learn more about how Curia can help your operation with rapid scale-up, from hundreds of grams to tens of kilograms, contact us directly here.